Plastic strapping
SigSorter Bundle ejection table for Zero Defects
Located behind the ISB Inline Bundle squaring and strapping machine the SigSorter bundle ejection table is controlled by the ISB PLC Unit. Any defective bundles identified by the upstream FFG units glue control camera and/or a print quality check camera are automatically removed, after strapping, by the ejection table. This ensures that any incorrectly glued or printed bundles do not pass to the palletising area aiding the objective of zero-defect product delivery to end-users.
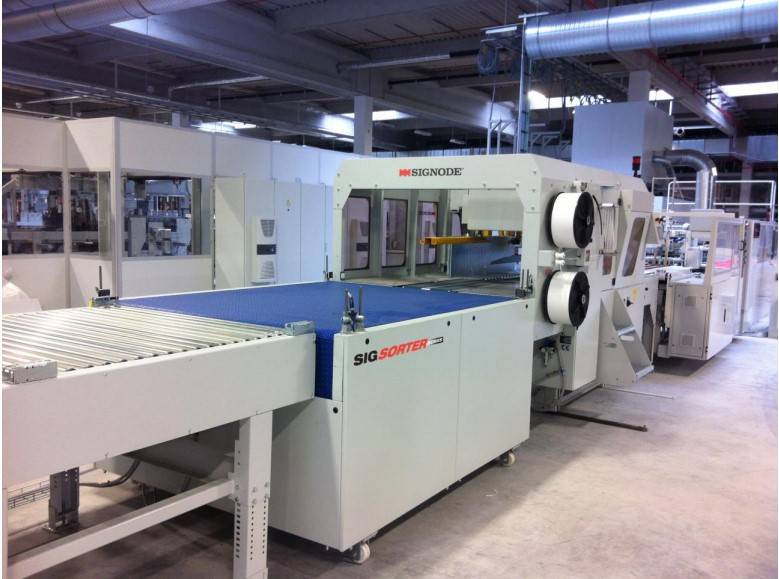
The MST -CE is a simple, easy-to-use semi-automatic strapping machine for low and medium volume packaging applications, incorporating many CE safety features for maximum operator protection.
The strap length is pre-selected to suit the size of the package, which is placed on the table top and positioned against the two guides. The strap is then pulled around the pack and mserted mto the strap insert slot, automatically initiating the strap cycle. It is automatically gripped by the strappmg head, tensioned, sealed and cut off.
At the end of each strap cycle, the strap is pre-fed through a strap channel in the middle of the table.
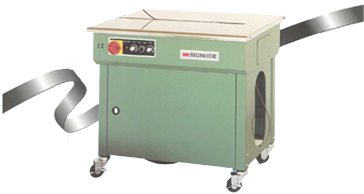
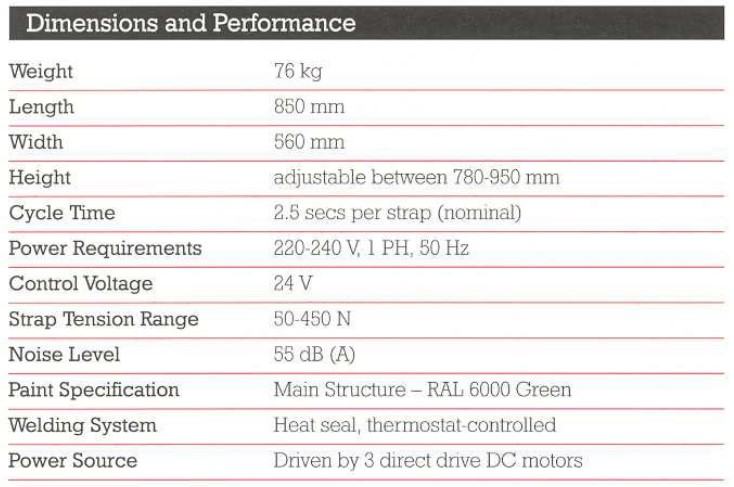
The LC-1000 low cost plastic strapping machine is designed for light to medium-duty general packaging operations. This operator controlled machine cycles up to 24 straps per minute, making it ideal for box, container and carton closure applications. The LC 1000 uses 9mm polypropylene strapping.
LC1000 FEATURES
- Flexible operation
- Cycle activation can be initiated by a start button on the control panel, or by a foot or table switch, enabling the operator to position the package with both hands.
- Operator friendly
- Automatic loading, combined with a quick change strap dispenser, simplifies coil changeovers.
- Simple tension control
- Roller tabletop
- Simplifies operation and reduces operator fatigue when pushing strapped product out of the machine onto exit conveyor.
- Built to full CE safety specifications
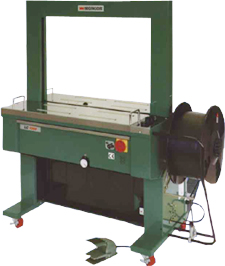
The AK-200 is a strapping head designed to be used in combination with various non metallic strap types and sizes.
The head is used in fully automatic strapping installations and it is suitable for a variety of applications in the steel, non ferrous, brick, block, panel and general packaging industries.
Head Features
- One-piece aluminium casting
- Robust design
- Fully electrically powered
- Power source (0.55 kw head motor, 0.75 kw tension weld motor)
- Off-center construction for easy service
- Cam control
- Unique strap feeding system reducing the number of strap jams considerably
- Large feed wheel # 207 mm, for better tension transmission
- Strap feed and take-up speed 1.25 m/sec (optional: up to 3 m/sec by inverter)
- Adjustable strap tension to 4500 N (optional up to 6000 N)
- Controllable strap overlap
- A minimum number of replacement parts
- Easy to maintain
- Min. package face 150 mm/optional 120 mm with short shutter 120 mm
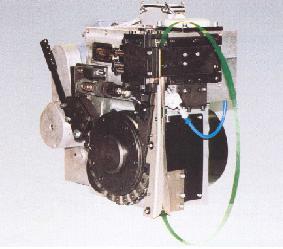
MH-TRB Top-Seal machine can strap varying sized products including very low loads and palletised loads on Euro as well as quarter pallets. The modern stable machine construction, modular design and a high focus on low-maintenance needs of the unit during conception ensure maximum uptime and the lowest total cost of ownership for customers, with maximum packaging and strapping efficiency and economy.
The Signode MH-TR modular top seal machine has been developed with a highly flexible design offering a wide range of machine options. The MH-TRB suits most customers needs to secure products on pallets and non-palletised loads using both PP and PET strapping materials. The head is top-mounted on the machine frame for optimum strap tension transmission onto the package and indexes onto the top of the load.
- High speed operation – to cater for high throughput production lines
- Fully enclosed telescopic chute system for high speed strap feed- fixes goods securely
- Maximum machine up-time – due to simple Modular MH head and feeder design
- Improved load securement & package stability – consistent strap tension on PP and PET materials
- Lower cost of ownership – easy service & low maintenance needs
- Easy module exchange – separate modules weigh 10 to 12,5 kg only
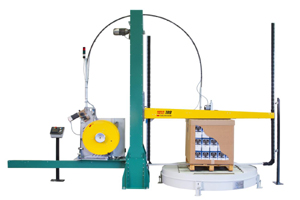
The Signode PSF is a power strap feeder specially designed to apply straps quickly and efficiently around palletised or other large packs. Manual strapping of large, or palletised loads, is labour intensive and extremely time consuming. In some instances it can place operatives in a hazardous position and often, to overcome this, two operatives are required to complete the procedure.
The Signode PSF provides a much faster and more efficient alternative to manual strapping. Only one operator is required with the Signode PSF, which also acts as a workstation, enabling all packaging operations to be completed in a safe and ergonomic position – literally at the touch of a button!
Included in the Signode PSF is a strapping tool located on an overhead spring pivoting system, ensuring the strapping tool is not only always in the right position, but is light to use, minimizing operator fatigue.
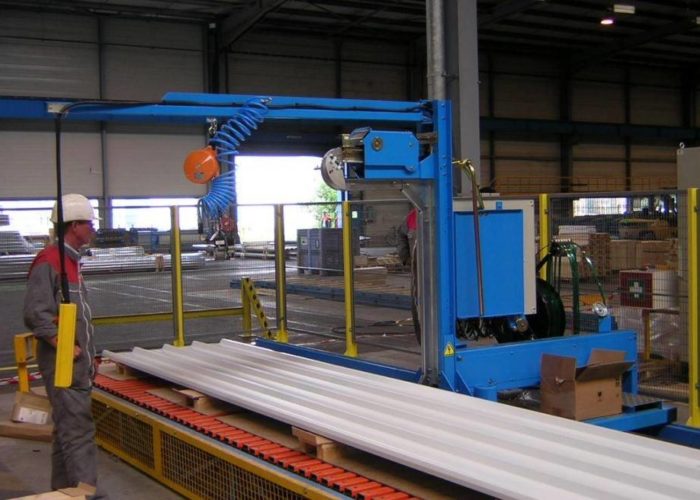
Extensively proven worldwide, with approaching 2000 successful machine placements, Signode ISB machines are universally acknowledged as the ‘industry standard’ bundle/squaring/strapping machine, both in terms of performance and reliability. Now, the new generation ISB offers casemakers even greater production efficiency combined with the reliable, high-speed, low-maintenance operation, for which ISB is renowned.
The ISB automatically squares and straps up to 32 bundles per minute, strapping in the flute direction. Now featuring even simpler construction and more durable parts, the ISB offers outstanding reliability – all in a more compact footprint reducing floor space requirements by 30% to accommodate longer casemaking lines.
ISB has been designed around a revolutionary new modular system to make it easier to choose the ideal system specification to suit customer requirements. The range comprises three primary models, the ISB 13,16 and 20 to accommodate all FFG widths. Models range from single pusher/single head economy model, to dual-headed machines with two independent pushers and fully automatic coil change, providing continuous availability.
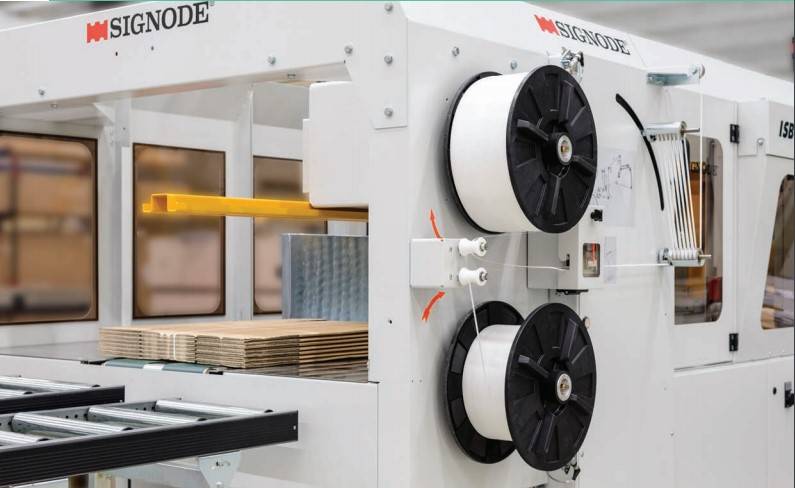
ISB Features
- Auto re-set feature
- Auto Re-set feature automatically adjusts the ISB to suit new stack dimensions at the push of a button.
- Modular design
- A unique modular concept with stack widths from 170 mm to 2000 mm, plus a full range of options allows you to choose the perfect system for your requirements.
- Automatic coil change
- Another Signode breakthrough. Strap is automatically spliced from a second dispenser to provide continuous production with zero downtime.
- Compact design
- Requiring 30% less floor space than previous models, ISB easily integrates into existing lines and facilitates the requirement for longer casemaking lines.
- Pre-drape strapping
- Machine uses economical narrow polypropylene strap with maximum efficiency, producing flat tight bundles that can be readily palletised.
- Unmatched simplicity
- New ISB design combines simplified construction with even more durable wear parts, for significantly reduced ownership cost.
The Next generation GCU-NG succeeds the well proven GCU first generation strapper. By using new improved and highly reliable components and materials in a modern design the press is simpler, faster and even more reliable for maximized machine uptime.
The modular design enables our customers to tailor-make their machine for their plants current and future needs. Some options are available for later installation as retrofits if required.
Industry standard performance and reliability for higher productivity and lower ownership cost.
GCU-NG 2500 FEATURES
- Greater productivity
- Standard up to 150 pallets an hour, high-speed version available.
- Next generation machine design
- Reduced service and maintenance needs, remote monitoring and lower energy needs.
- Fits customers exact needs
- Modular design with options for todays and tomorrows demands.
- High productivity and safety
- Automatic strap loading and Edge protection reloading from outside guarded area so non-stop operations.
- Very easy to use
- Intuitive, simple, easy to use, icon-driven operator HMI, simple packaging programme changes.
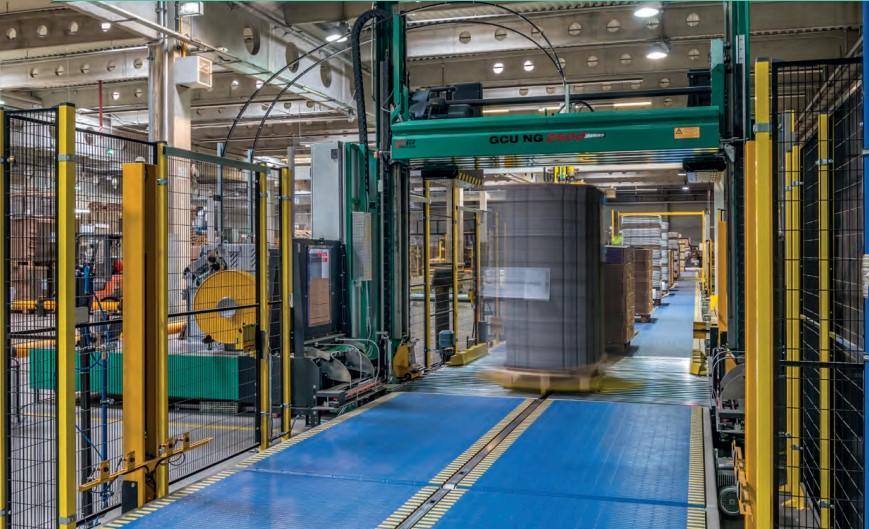
The SIGCorr Strapping Station for multipoint glued and crash-locked boxes
The Signode SIGCorr is the most advanced combined bundle squarer/strapper of its type currently available on the market. It is the most reliable and economical solution for the corrugated industry. Specific models are available to suit all requirements. The unit is a strapping station specifically developed for multipoint glued and crash-locked cartons packaging.
Every aspect of the Signode SIGCorr is designed to maximize productivity. All machines feature automatic squaring and strapping of up to 30 bundles per minute. When double strapped the capacity is 17 bundles / minute. A range of options are also available to ensure the machine is perfectly designed for each customer’s unique production, product and their end-users requirements.
SIGCorr benefits
- Versatile
- For strapping 3, 4 & multi-point glued boxes
- User friendly, intuitive controls
- Maximum machine uptime
- Up to 30 bundles per minute
- Significantly reduced bundle scuffing, marking during packaging
- Easy access and simple strapping module removal
- Highly profitable
- Reduced personnel needs in semi-auto mode
- Stable bundles
- By accurate bundle compression & consistent strap tension
- Case/Bundle Format change in less than 2 minutes, set-up from memory
- High productivity
- Quick format change and set up in under 2 minutes
- Can store up to 2500 different box formats
- Soft-touch product handling through driven belts no rollers
- Can also handle RRP and SRP
- Improved multipoint gluer speed & throughput as SIGCorr can handle more bundles
- Faster ROI due to increased productivity at lower costs
- SIGCorr takes the cases from the operator and processes the bundle and is flexible and adaptable to all specific product requirements
- Reduced issues of repetitive strain injury, operator fatigue and improved overall workplace safety due to inherent machine design
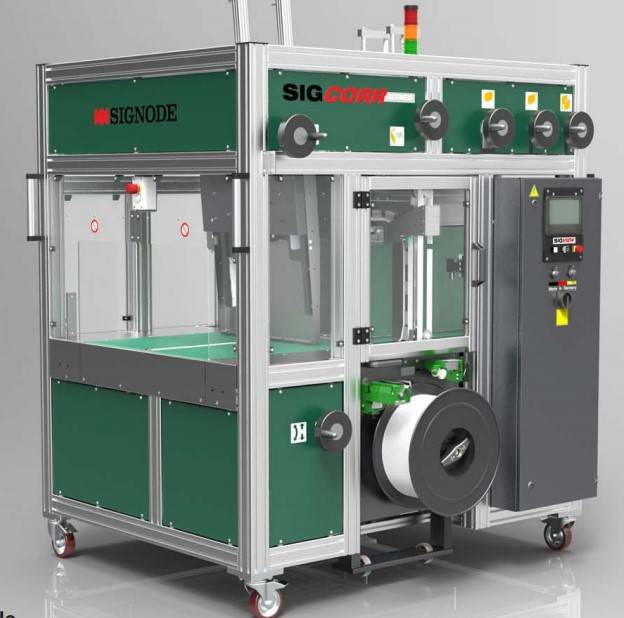
SBM 4000 Series
The SBM 4000 series is designed to use 9 and 12mm embossed Polypropylene strapping. The Signode Dylastic range of SBM 940 / 955 / 1240 / 1255 products offer economic and reliable strapping operations, less coil changes due to more meters of strap per coil, and thus higher machine uptime and availability.
Unique jam-resistant technology
The patented SBM strapping head offers the highest level of reliability currently available.
High speed strapping
Fast strapping cycle – up to 70 straps per minute – increases productivity potential.
Easy strap loading
With up to 70 straps per minute, the SBM 4000 provides the highest available speed in the range of general duty machines using 9 and 12mm economic Dylastic® embossed (PP) Polypropylene strapping
Easy maintenance
The strap path is fully accessible, no belts or clutches, most of the maintenance work can be executed without the use of any tools. There are few if any machine settings which can or need to be adjusted on the machine.
Automatic strap re-feed
Any time the strap doesn’t go around the package, a simple step on the foot pedal, and the machine clears itself. If the machine is cycled without a package in the machine it kicks out a strap loop to self clear.
Easy coil loading and error free dispenser, located inside the machine for customer with space issues to make the machine easier and simpler to use in smaller plants.
The strap coil pays off easily from the marked direction so loading a new coil of strap becomes simpler than ever, also due to the easy lock dispenser side cover.
Easy Accessible Strap Path
The hinged table top provides easy and fast access to the strap path. By lifting the guide, full access to the strap path is obtained – without tools.
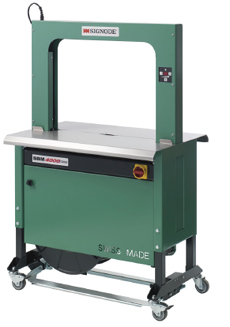
The Signode SBM 4300 is an automatic, operator controlled strapping machine that is arguably the simplest machine to use and maintain currently available. The strap dispenser on this model is located on the outside of the unit for very easy strap coil reloading and access.
With far fewer components, compared to previous models, plus industry leading features that increase productivity and reduce downtime, SBM 4300 creates the opportunity for production throughputs of up to 70 straps per minute!
By eliminating the use of drive belts drive chains and clutches, wear parts have been significantly reduced on the SBM 4300, creating a machine that combines ease of operation with low cost of ownership.
SBM 4300 Main Features
Jam-resistant technology
Patented SBM strapping head provides industry leading packaging reliability.
High speed strapping
Fast strapping cycle – up to 70 straps per minute – increases productivity potential.
Easy strap loading
Strap loads from the indicated direction eliminating down time and waste strap.
Low maintenance
Easy access, far less components and ‘tool free’ service mean lower costs.
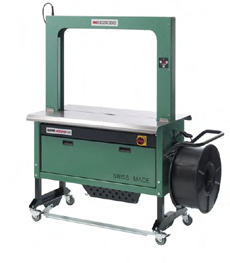
The Signode SBM 4330 is a fully automatic, operatorless strapping machine that is the simplest machine to use and maintain currently available.
With fewer components, compared to previous models, plus industry leading features that increase productivity and reduce downtime, SBM 4330 creates the opportunity for production throughputs of up to 70 straps per minute!
By eliminating the use of drive belts chains, and clutches, wear parts have been significantly reduced on the unit, creating a machine that combines ease of operation with low cost of ownership.
SBM 4330 Main Features
Jam-resistant technology
Patented SBM strapping head provides industry leading packaging reliability.
High speed strapping
Fast strapping cycle – up to 70 straps per minute – increases productivity potential.
Easy strap loading
Strap loads in the indicated direction eliminating down time and waste strap, with the easy lock strap dispenser cover making the coil change very easy.
Variable speed conveyor
Standard variable speed reversible conveyor integrates easily into existing conveyor system.
Low maintenance
Easy access, less components and ‘tool-free’ service mean lower costs.
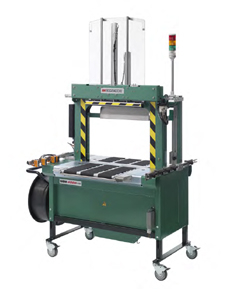
SBM 4301 Short anvil model
In order to accommodate very specific application needs in various industries Signode has developed from its standard machine range the new 4301 version which is a small frame, short anvil model. The short strapping anvil enables products to be strapped with have a small face of only 50mm wide and as low as 5 mm. Products in small bundles such as timber millwork, veneers, rounds, wooden profiles, battens, facias, plastic pipes, plastic profiles, aluminium profiles or bundles of special engineering steel or cable trays etc can be securely strapped for transport using 9-12 mm Dylastic® SBM 940/955 and Dylastic® SBM 1240 and 1255 Polypropylene strapping.
The thinner gauge strapping used on these models from 0,4 to 0, 5mm gauge enables economic strapping compared to other models using 0,6-0,9 mm gauge materials and reduces coil change-over times due to greater strap meterage per coil and contributes to overall machine uptime increases and availability.
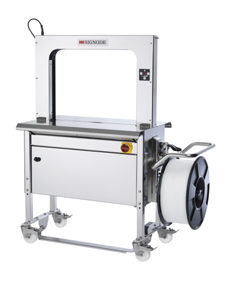
SBM 4332 in Stainless Steel finish
Designed to take into account the strict hygiene requirements of the meat and poultry processing sector and also to facilitate easy machine wipe-down, the SBM 4332 model has be designed with many parts from high-quality stainless steel. The main machine framework, chute, table top, exterior panels and various internal machine panels are manufactured from heavy-gauge stainless steel plate for maximum durability and high corrosion resistance. Available as a basic fully automatic machine the SBM 4322 can also be equipped with conveyor belts and top load compression bar and many other options for integration into fully automatic meat, poultry and other food packaging lines. All these products in polystyrene boxes, corrugated and solid board cartons or trays can be safely strapped with 9-12 mm Polypropylene strapping, to fulfil most customers produce packaging requirements.
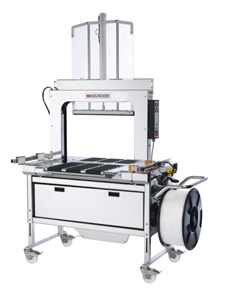
SBM 4300 & 4330 Large Frame Machines and a series
The SBM Large Frame model is ideally suited to strap very wide and flat products using 9-12 mm heavy-duty, but cost-effective Polypropylene strapping. The machine is available in two main chute sizes. This covers most applications needs for large flat-pack furniture, doors and panels for high speed package strapping operations. The accurately tensioned strapping securing closes the cartons or corrugated product packaging materials for stable, transportable loads. The unit is available with a large range of machine options for optimum strapping performance and can be supplied as a fully automatic operator controlled machine or as an inline automatic and operator-less model integrated into a customers end of line packaging system. For logistic centres and customer layouts where products enter the machine in various orientations both centreline and on a fixed pass-line the SBM can be supplied with a strapping head located off centre in the so called SBM 4330-A versions, to accommodate these products and customer layout.
The Signode SBM 4400 is a new machine in the SBM range not available in the previous series. The SBM 4400 model it an automatic, operator controlled strapping machine with the strapping head integrated as a side-seal model in the side of the machine housing that is arguably the simplest machine to use and maintain currently available. The strap dispenser on this model is located on the rear of the unit for very easy access and simple insertion of the strap end into the machine automatically loads the strap into the chute and the machine accumulator box.
By eliminating the use of drive belts drive chains and clutches, wear parts have been significantly reduced on the SBM 4400/4401, creating a machine that combines ease of operation with low cost of ownership.
The SBM 4401 unit is equipped with the short anvil head which enables boxes and other products to be strapped by the machine with a height as low as only 20 mm and 100 mm wide. The standard SBM 4400 can accommodate loads as small as 50 mm high and 100 mm wide.
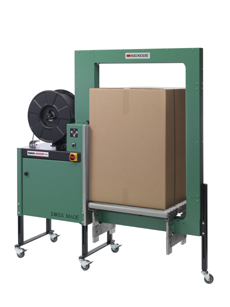
SBM 4400/4401 Main Features
Jam-resistant technology
Patented SBM strapping head provides industry leading packaging reliability.
High speed strapping
Fast strapping cycle – up to 70 straps per minute – increases productivity potential.
Easy strap loading
Strap loads from the indicated direction eliminating down time and waste strap.
Low maintenance
Easy access, far less components and ‘tool free’ service mean lower costs.
SBM 2000 Series
The SBM 2000 offers unique levels of speed and reliability, together with an outstanding simplicity of design. This makes the SBM 2000 to be a truly top choice for general duty light-duty strapping applications.
SBM 2000 Main Features
Unique jam-resistant technology
The patented SBM strapping head offers the highest level of reliability currently available.
High speed strapping
With up to 70 straps per minute, the SBM 2000 provides the highest available speed in the range of general duty machines.
Easy maintenance
The strap path is fully accessible, no belts or clutches, most of the maintenance work can be executed without the use of any tools.
Automatic strap re-feed
Any time the strap doesn’t go around the package, a simple step on the foot pedal and the machine clears itself. If the machine is cycled without a package in the machine it kicks out a strap loop to self clear.
Easy coil loading and error free dispenser
Easy coil loading and error free dispenser, located inside the machine for customer with space issues to make the machine easier and simpler to use in smaller plants.
The strap coil pays off easily from the marked direction so loading a new coil of strap becomes simpler than ever, also due to the easy lock dispenser side cover.
Easy Accessible Strap Path
The hinged table top provides easy and fast access to the strap path. By lifting the guide, full access to the strap path is obtained – without tools.
PN2-114
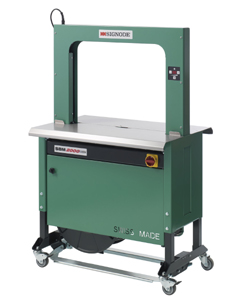
The Signode SBM 2300 is an automatic, operator controlled strapping machine that is arguably the simplest machine to use and maintain currently available.
With far fewer components, compared to previous models, plus industry leading features that increase productivity and reduce downtime, SBM 2300 creates the opportunity for production throughputs of up to 70 straps per minute.
The SBM is controlled via a simple, easy to use and understand HMI with strap tension adjustment, heat knife temperature adjustment and operator fault codes information display on the machine control panel, reducing the need for any operator training or any re-training.
By eliminating the use of drive belts and clutches, wear parts have been significantly reduced on the SBM 2300, creating a machine that combines ease of operation with low cost of ownership.
Jam-resistant technology
Patented SBM strapping head provides industry-leading packaging reliability.
High speed strapping
Fast strapping cycle – up to 70 straps per minute – increases productivity potential.
Easy strap loading
Strap loads from indicated direction eliminating down time and waste strap, easy strap loading with easy lock strap dispenser cover.
Low maintenance
Easy access to whole machine, and less components and ‘tool-free’ service mean lower costs.
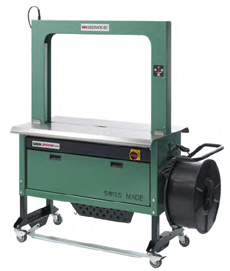
The Signode SBM 2330 brings high speed, fully automatic strapping to light duty packaging applications. With cycle times of up to 70 straps per minute, plus a range of advanced features, designed to eliminate unplanned downtime, LBX 2230 is the machine to achieve maximum productivity potential. And with far fewer components, compared to previous models, plus the elimination of wear parts, such as drive belts, chains and clutches, with the SBM 2330, Signode have created a strapping machine that combines ease of operation with low cost of ownership.
SBM 2330 Features
Jam-resistant technology
Patented SBM strapping head provides industry-leading packaging reliability.
High speed strapping
Fast strapping cycle – up to 70 straps per minute – increases productivity potential.
Easy strap loading
Strap loads from indicated direction eliminating down time and waste strap and the dispensers is equipped with an easy-lock side cover.
Variable speed conveyor
Standard variable speed reversible conveyor integrates easily into existing conveyor system.
Low maintenance
Easy access, less components and ‘tool-free’ service mean lower costs.
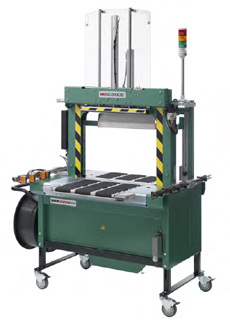
SBM 2301 Short-anvil model for small products
In order to accommodate very specific application needs in various industries Signode has developed from its standard machine range the new SBM 2301 model which is a small frame, short anvil model. The short strapping anvil enables products to be strapped with have a small face of only 50 mm wide and as low as 5mm. Products in small bundles such as money bundles in cash centres, letters, timber millwork, veneers, battens, small plastic pipes or wire cables, hoses, cable trays etc and small aluminium profiles can be securely strapped for transport and handling using 5 mm Dylastic® SBM 540 Polypropylene strapping.
The SBM range is the simplest most reliable operatorless strapping machine currently available in the corrugated industry. With 40% fewer parts compared to previous models it is also the simplest to use and maintain.
With industry leading features that raise productivity and reduce downtime, the SBM range offers the potential for production throughputs of up to 70 straps per minute.
By eliminating the use of belts, clutches or pulleys from the strapping head, wear parts have also been significantly reduced, creating a machine that combines easy maintenance with low cost of ownership.
SBM RANGE FEATURES
Automatic strap feed and refeed
Patented Signode technology ejects a mis-fed strap, then rethreads and continues strapping without minmal operator intervention.
Simple single direction strap feed
Out of strap feature
Automatically ejects the remaining strap tail at the end of each coil, eliminating the downtime required to remove excess strap in the machine.
Automatic strap loading
Strap is loaded automatically simply by the lift of a lever
Total accessibility
The strap path on the SBM range is fully accessible without the need for tools. Just raise the table top and lift the guide for access to the strap path. It’s that simple!
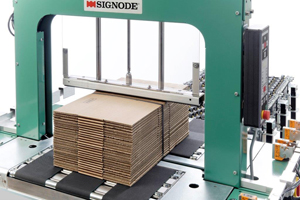
MH Series
The Signode MH-V modular side seal machine has been built with a highly flexible design with a wide range of machine options and strapping chutes sizes. The MH-V suits most customers needs to secure the packaging materials or type of carton packed products such as domestic appliances, kitchen cabinets, boilers or also other stretch or shrink-wrap packaged products using both PP and PET strapping materials.
Features and benefits
High Speed unit
High production throughputs strap feed speed 3m/sec – to cater for high throughput production lines Easily accessible strap path. Auto strap re-feed from dispenser into sealer unit head – for reduced operator effort. Self-clearing, auto strap re-feed to take up and re-feed the strap into the machine chute.
Robust design
Maximum machine up-time – due to the simple Modular MHC head with separate strap feeder and sealer modules machine uptime, productivity and TCO can all be maximised.
Easy module exchange- the separate modules weigh only 12,5 kg each at most and can be removed and replaced in the machine in less than a minute without the need for tools.
Low package capability
Highly flexible system to adapt to varying customer product sizes in one machine Minimum package height of only 200mm, maximum package height 2.800mm Package width 500mm to maximum 2.000mm.
Variable and consistent strap tension
Strap tension can be infinitely adjusted to suit most customers’ products from low for sensitive Products up to high tension levels. The tension ranges from 80 N to 900 N for improved load securement and package stability.
Low Cost of ownership
Lower cost of ownership due to easy service access, low maintenance needs due to direct electrical drive motors, no chains, v-belts, timers, proximity switches etc on the strapping modules.
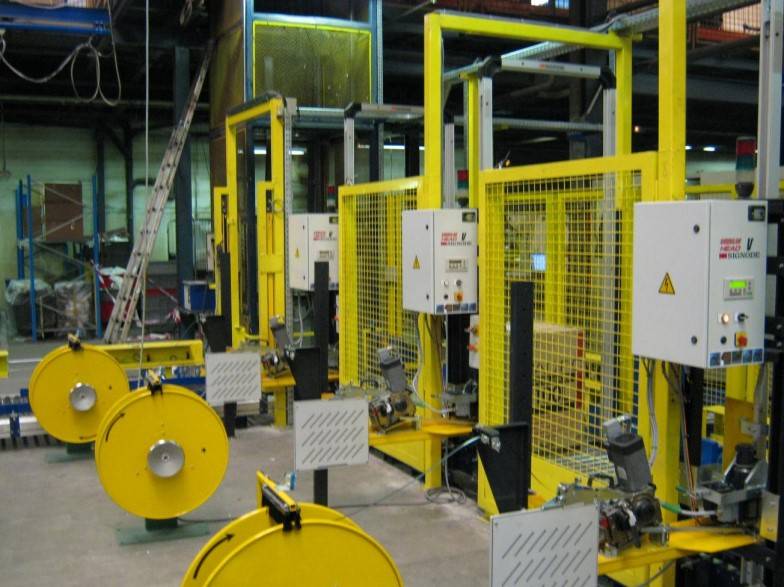
Similar in design to the MH-V the MH-VR has an indexing strapping head which moves onto the side of the load during the strapping operations to cater for varying package widths. The head stroke is 500mm, enabling a large variation in load sizes to be easily accommodated. The MH-VR has a wide range of machine options with strapping dispensers for 200 or 406mm cores, quick exchange strap dispenser units, twin units for very high throughput operations and also a spare sealer unit for rotational and preventative maintenance systems.
Features and benefits
Compact Machine Design
The narrow design of the machine and the modular aluminium strapping chute enables the Machine to be easily integrated into new and existing customer handling systems where space may be at a premium.
Simple low service needs
With the easy lock-in modules which can be removed without tools in less than 20 seconds any service needs can be completed simply and effectively off line without interrupting the production. All machine settings can be adjusted via the integrated TD 200 display unit.
Maximum Safety
The machine has full CE certification and can be supplied with machine safety guarding and also light guard options to suit most customer plants and national safety needs for maximum operator safety and protection.
Flexible Strapping Material Options
The MH range with its MHC vibration weld head can accommodate a wide range of both Polypropylene and Polyester strapping from 9mm to 12mm widths to suit a wide range of light to medium duty applications. The vibration weld head can be used with both types of strapping and does not generate any smoke or fumes during the welding cycle.
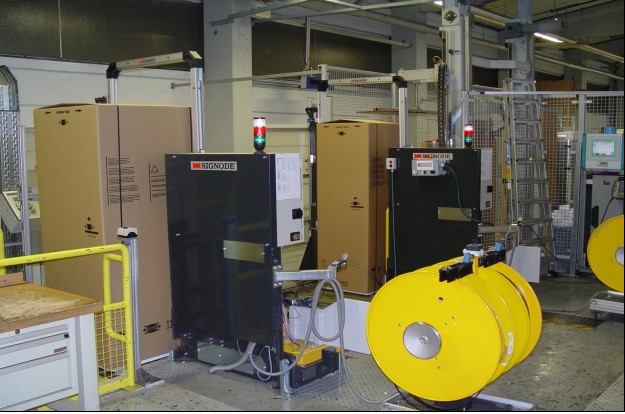
The Signode MH-VRB modular side seal machine has been developed with a highly flexible design offering a wide range of machine options.The MH-VRB suits most customers needs to secure packaging materials, cartoned goods or crates onto pallets using both PP and PET strapping materials.
The machine is built as standard with heavy duty aluminium,strap chute flaps for high-speed strap feeding and accurate and importantly vertical strap positioning onto the load. Strap chute built to suit each customer application. The strap auto-feed from dispenser into the sealer unit head reduces operator effort The standard strapping head is the MHCModular head for heavy-duty 9-12mm Dylastic® PP or Tenax® PET polyester strapping.
Features and benefits
High speed operation
To cater for high throughput production lines.
Frequency controlled bayonet for through the pallet strapping
Fixes goods securely to pallets.
Maximum machine up-time
Due to simplemodular MHChead and feeder design.
Improved load securement & package stability
Consistent strap tension on PP and PET materials.
Lower cost of ownership
Easy service & low maintenance needs.
Easy module exchange
Separate modules weigh 10 to 12,5 kg only.
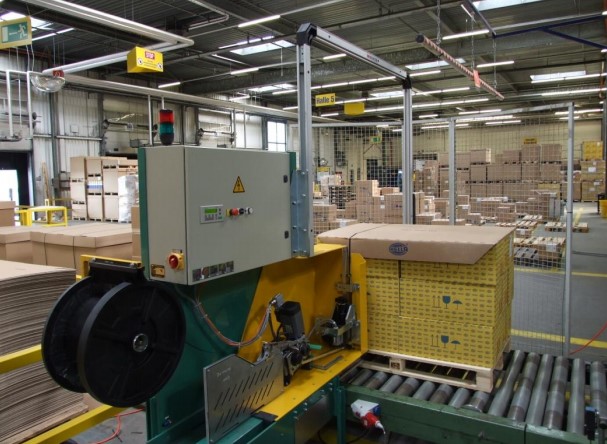
The machine is built as standard with heavy duty, full steel strap chute and chute flaps for high-speed strap feeding and strap guide bands for accurate horizontal strap positioning onto the load. The standard strapping MH head is designed for heavy-duty 9 -12mm Tenax® PET polyester and Dylastic® PP strapping. High strap tension version for 16mm strapping.
It features the easy-load, powered dispensers with automatic strap feed-up into the sealing unit.. The whole unit has a simple easy, to use free-standing machine control panel.
The MH-H can be used in a wide range of applications in the Construction, Furniture, Bottle, Logistics and Appliance segments to name but a few.
Features and benefits
Optimum pack protection
Torque motor drive for both outrigger and chute ensures optimum approach speed for maximum pack protection.
Easy to adjust
Up to 8 different strapping positions can be set in 8 different programmes as standard during commissioning in order to apply different strapping patterns to a range of products.
Easy to use
Simple intuitive HMI touch-screen panel to adjust al machine parameters, to provide pre-warnings, service assistance and service diagnosis without a programming unit.
Greater machine availability
Strap auto-load and auto-rewind facilities, plus quick-change strap dispenser system significantly reduces downtime when changing strap coils. Modular head systems enable units to be exchanged within 2 minutes for optimum machine uptime.
Adjustable strap tension
Offers tension levels from 100 to 900N for 9-11 mm and for 13- 16mm strapping up to 2.000N strap tension.
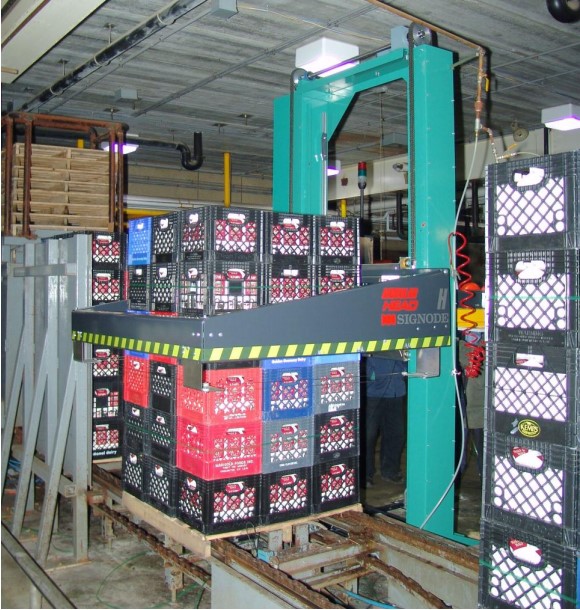
MH Modular Two Piece Head
The MH modular head is a completely new approach to strapping head design; as it is composed of two easy to handle and easy to use modules. The smaller lightweight, but robust sealer module for example weighs only 10 kg and can be easily removed from the machine for quick and easy maintenance.
The MH is used in fully automatic strapping installations and it is suitable for a variety of applications in the corrugated, paper, furniture, non-ferrous, brick, block, panel and general packaging industries.
Modular Head Features
One-piece simple robust design for each module
Lightweight as only 10-12 kg each
Fully electrically powered with quick-change plug attachments
Use both PP and PET Signode flat and also embossed strapping
Vibration-weld and heat-knife strap sealing options available
Maximum machine uptime as easy to change-out
Unique strap auto re-feeding system reduces the number of strap jams
Automatic strap feed up to head in high through-put machine models
Strap feed and take-up speed 3 m/sec (optional: up to 8 m/sec as high speed version
Adjustable strap tension to 900 N for 9-11mm and up to 2.000 N for 13-16mm strap width versions
Controllable minimal strap overlap and high-strength strap joint welds
A minimum number of replacement parts
Easy to maintain with only two simple tools
High quality parts for reduced wear means low cost of ownership
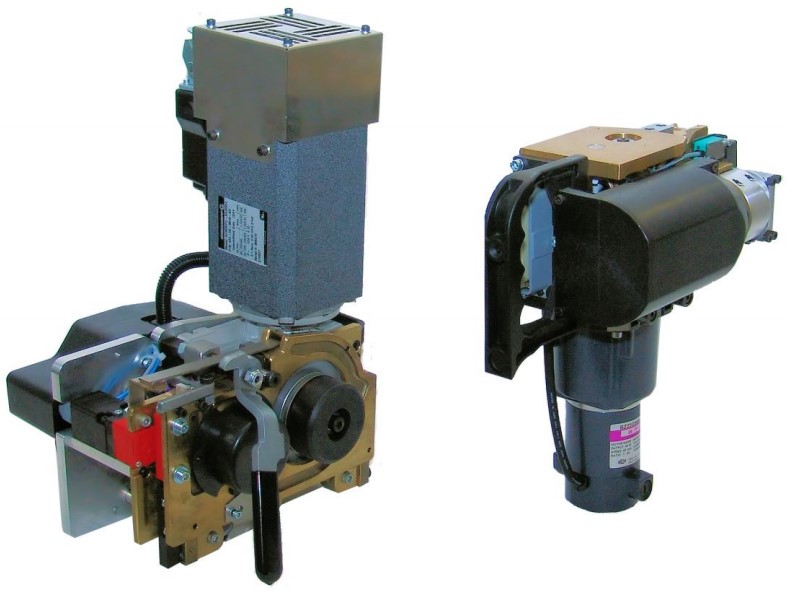