PRODUCTION AUTOMATIZATION EQUIPMENT (MINDA)
Intralogistics. Automatization of Plants. Conveying.
As the specialist for mechanical engineering our principal company MINDA develops and manufactures customized intralogistic systems for corrugated board, solid board, and paper industry, as well as complete plants, and equipment for lumber industry and transport lines and logistics systems for piece goods.
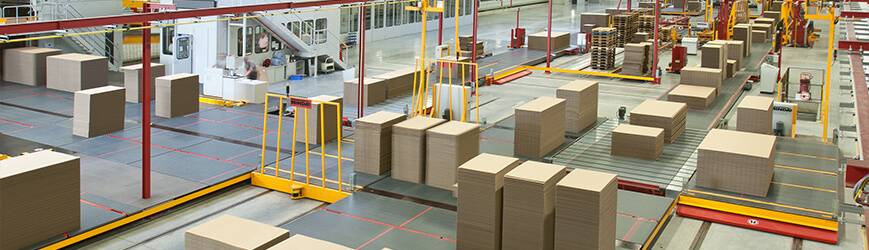
MINDA has been manufacturing automated intralogistic systems for the corrugated, solid board and paper industry, complete plants for the solid timber industry and solutions for general materials handling technology for more than 35 years.
In whatever area – raw material transport, production buffer storage systems, integration of converting machines or pallet loading centres for finished goods – we will not give you an off-the-shelf, standard product, but an individually customised solution.
We guarantee solid production technology including specially developed software solutions as well as installation and commissioning in time by our staff. The after sales service is a matter of course. We integrate our know-how into each project as a partner for our customers.
Automatic paper reel transport: transport system for paper reels, newsprints and coils
Apart from feeding the paper reels to the Corrugator, MINDA also provides return sections to the raw material warehouse, storage lines in high-rack warehouses and reel handling from the winder to the equipment.
The scope of supply includes the following components:
• preparation stations
• electronic scales
• underfloor carriages
• plastic chain conveyors for lying and upright reels
• transfer cars
• lifting devices for residual reels in the unwind stand
• upenders
The weight and the barcode of the paper reels are registered and integrated into the process of the material flow control.
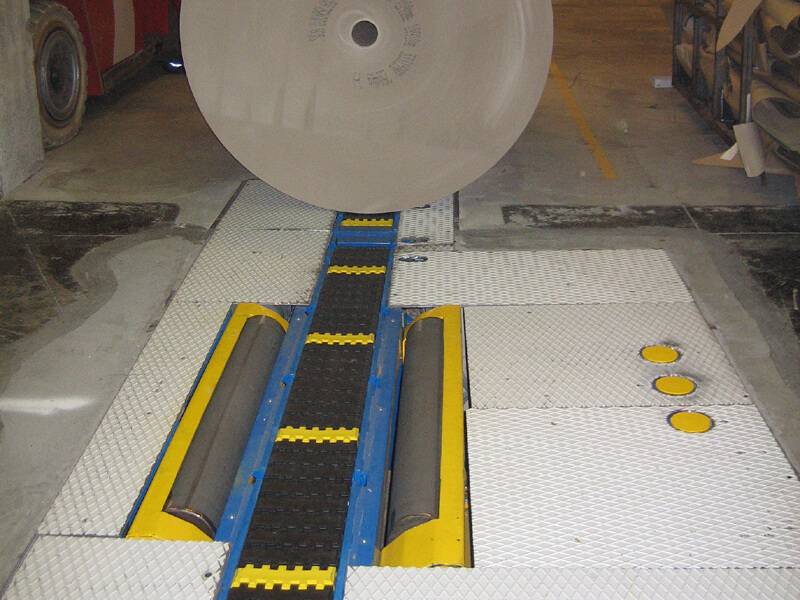
In order to ensure a fast and smooth transport of the stacks from the Corrugator, the stacks are optimized to blocs.
Depending on the goods to be transported, a maximum utilization of the transport capacities are provided. Thus the goods quickly reach the intermediate storage, the finished goods area or the dispatch department.
Automatic transport of stacks from the corrugator into the intermediate storage:
Different designs for stack transport in the intermediate storage, in the finished goods area and in the despatch warehouse are available.
Advantages:
+speed up to 150 m/min
+several conveyors to pick up goods of different orders
+vulcollan wheels / servo drive for vibration-free running
+sinusoidal acceleration and braking for smooth start and stop for optimal transport
Plastic chain conveyor as transport elements:
The plastic chain conveyors, which have been successfully used since 1999, displaced driven roller conveyors nearly completely from the market due to their numerous advantages. They allow to transport the stacks from the corrugator to the converting machines and to transport the stacks as semi-finished or finished goods directly to the despatch.
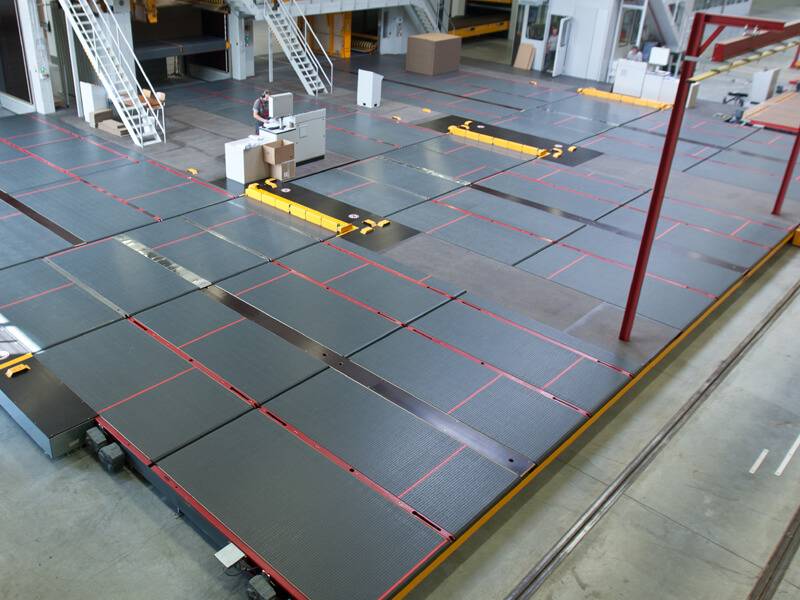
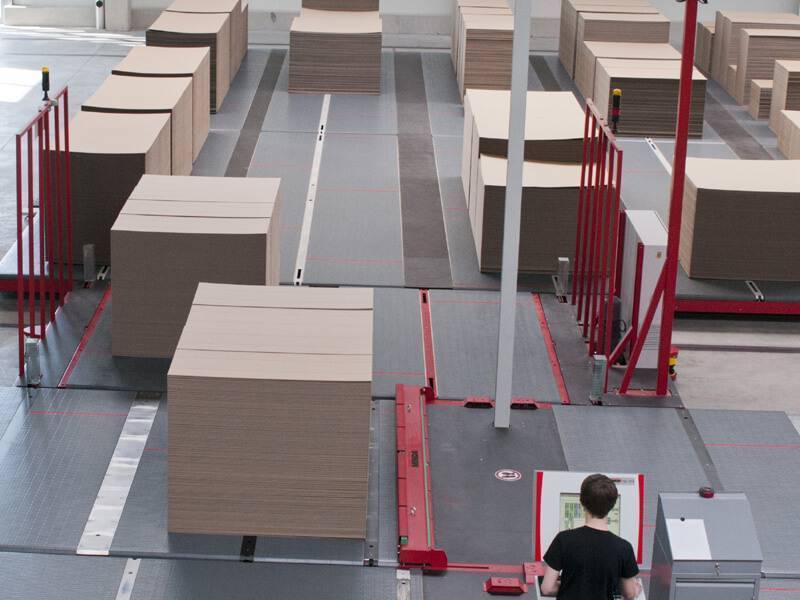
Intermediate storages are used when sheets, sheet plant delivery and semi-finished goods are to be stored and re-sorted as well as for drying corrugated cardboard during the production process or when an order-related supply of converting machines is to be ensured.
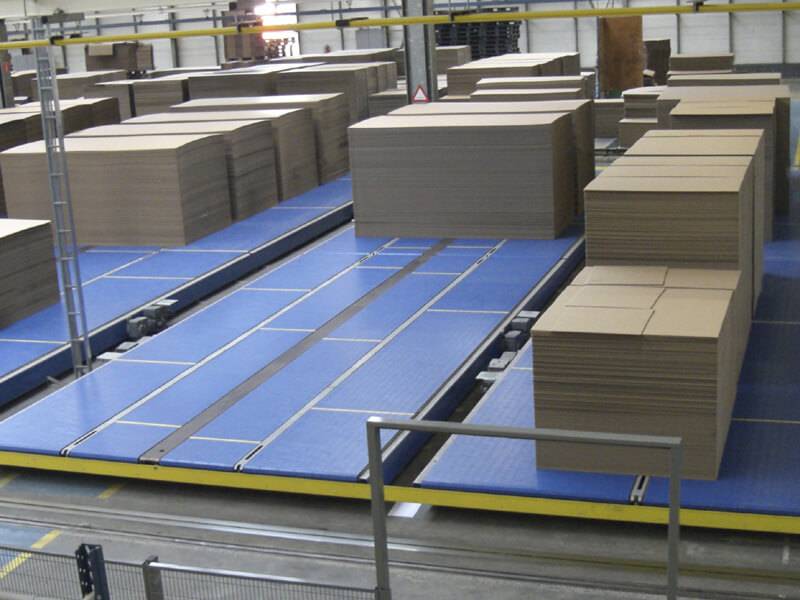
Vertical lifts connect two or more levels in order to return tools, printing plates and colours back into the warehouse.
They can also be used for heavy unit loads.
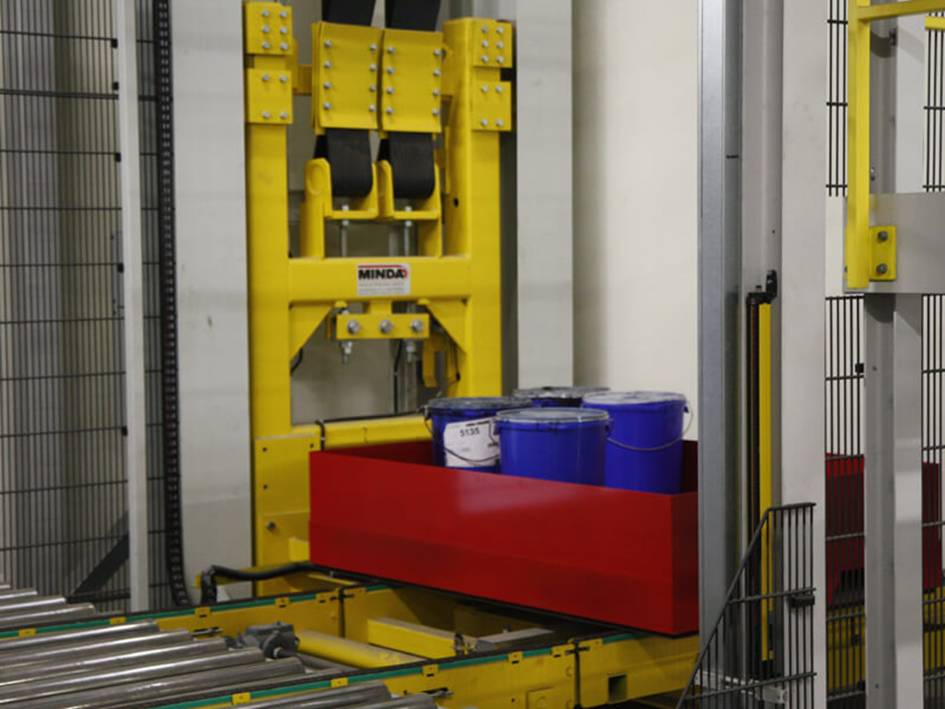
Depalletisers provide the defined outfeed of cardboard stacks from pallets. At the same time, the empty pallet is laterally fed out and can be picked up by the forklift truck.
They are used in front of converting machines or in front of intermediate storages for sheet supply.
The empty pallets can be stacked in a pallet magazine.
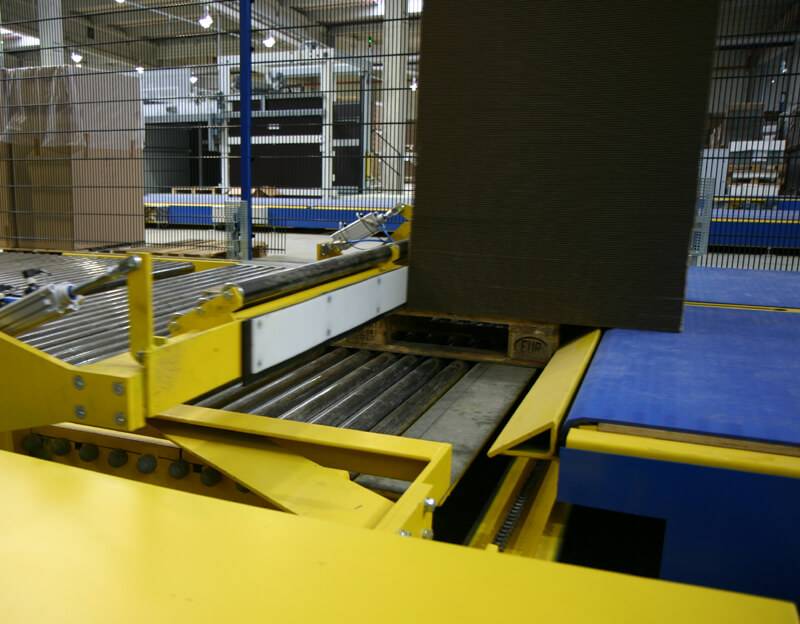
Turning devices are used in the production flow, when the transport direction is changed or the length-width ratio of the goods is to be changed for the further production.
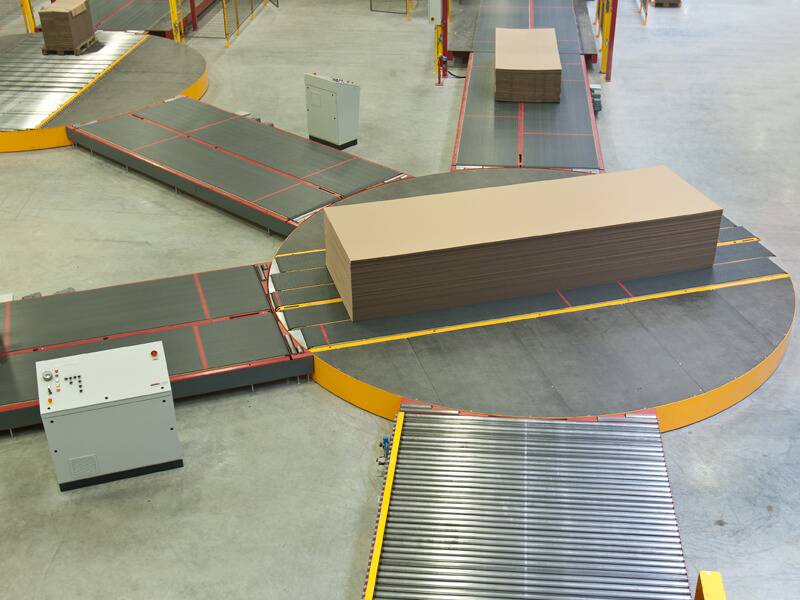
The ADVECTORprefeeder ensures an optimized feeding of printing lines, inliners, flat-bed and rotational die-cutters by creating a continuous shingling sheet flow.
Its extremely short installation length, achieved by the lateral infeed, provides a nearly universal application – even under very constricted space conditions.
In contrast to conventional solutions the stacks are not lifted but directly processed in small packages. An integrated turning device allows the operator to decide if due to production the package is to be turned. An intermediate buffer ensures that the shingling sheet flow is not interrupted. The new pushing process with its parallel stack change leads to a throughput rate of up to 24,000 sheets per hour.
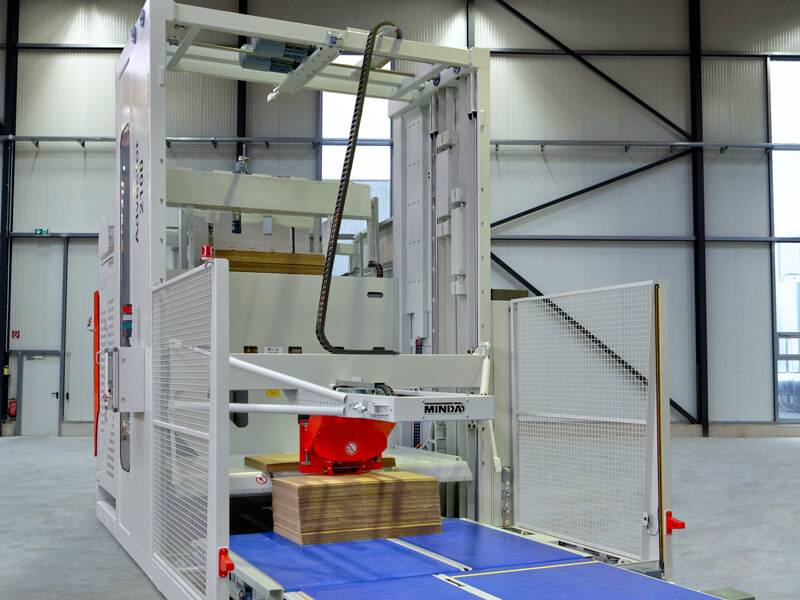
For completion of palletizing lines in the area of flat-bed and rotational die-cutters we have developed the Breater MIBreak for different working widths up to 3,200 mm. The breaker is used to separate die-cut sheets, when several finished products are produced from one die-cut sheet and must then be separated after the die-cutting process. The electronically working Breaker MiBreak with adjustable and segmented bar features a high positioning accuracy and a simple operation. It is also suitable for L-form nesting. Due to the rubber-covered plastic chain only a low pressure is required so that the flutes of the sheets are not compressed during the separation process.
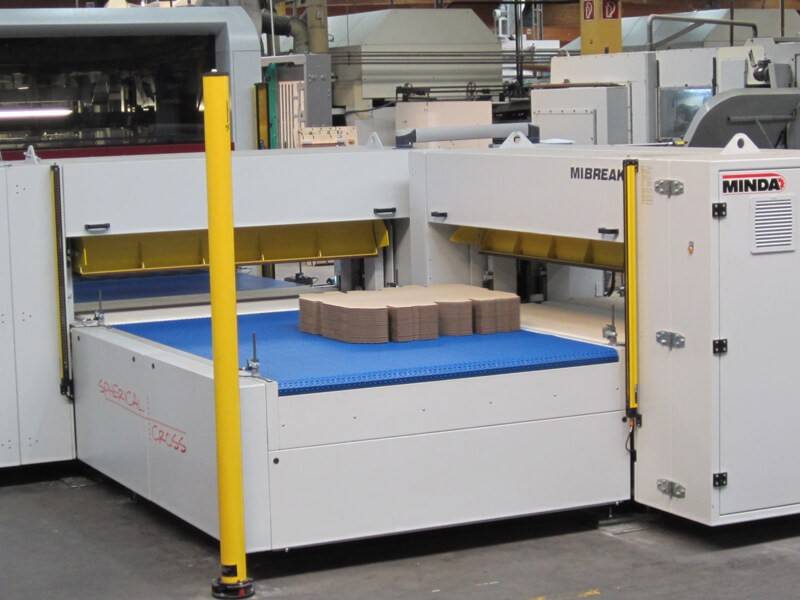
MINDA distinguishes between stack turners turning in or crosswise to the transport direction.
Stack turners turning in transport direction are used to turn stacks in front of or behind printing machines. They turn stacks up to 2 t with and without pallets in minimal cycle time and can also be operated in throughfeed operation. Moreover, the turner can palletize oder depalletize the stacks.
Stack turners turning crosswise to the transport direction are mainly used in the finished goods transport. The stack is gently clamped and turned by 180°. The following stack is directly fed into the turner and can be turned, as the turning drum does not have to be returned. This system is only used in throughfeed operation and turns stacks up to 1 t.
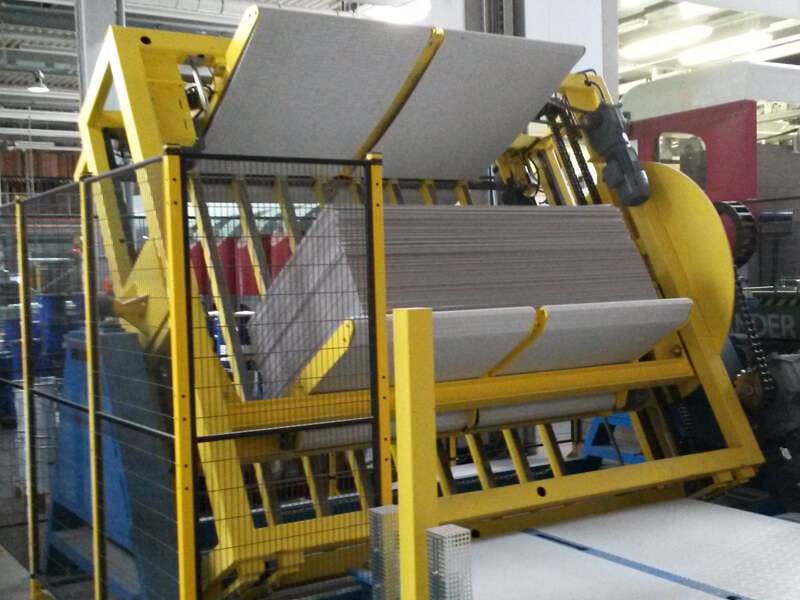
The robot for load forming is used for fully-automatic creation of stacks behind inliners, flat-bed die-cutters and rotational die-cutters.
The bundles are automatically fed to the robot and can be turned, rotated and doubled. The robot gripping system allows to pick-up one or several bundles at the same time and properly deposits them.
The automatic dispension of bottom sheets and intermediate sheets is effected via a linear unit with injection suction devices.
The automatic dispension and application of pallet labels is possible.

Pallet loading stations transfer goods without pallets onto pallets and they are used for sheets as well as for finished goods.
MINDA provides single and double loading stations. Double loading stations are capable of depositing on pallets a maximum of 200 loads per hour (max. block length 2 x 2.4 m or 1 x 5.0 m).
Advantages:
+no pallets in the processing area
+precise and careful pallet loading
+smooth lowering of the goods onto the pallet, automatic adaptation to the current pallet height
+pallet positioning precision: +/- 15 mm in relation to the goods
+fold-on device for bottom protection sheets
+especially compact design
+electrical drives
Linear robots ensure the preparation of empty pallets for the pallet loading station.
Fold-on process
The protection sheets are exactly unfolded at the block by means of independently controlled flaps so that they are closely applied in case of a later strapping process and provide an optimal protection of the goods.
Finally the loaded pallet with protection sheet is transported to the strapping process.

There is a complex control process behind the flexibility and the size of these intralogistics processes. This process also includes software solutions optimally adjusted to the individual conditions.
They are based on MINDA MoveIT, the control and visualization system for intralogistics programmed by MINDA.
The system coodinates the control of transport sections, floor conveyors and packing devices according to the plans of the ERP system.
This superordinated control based on PC is further internally developed by experienced programmers.
MINDA MoveIT guarantees a fully-automatic operation in all transport sections. The transport operations are optimized so that all storing places are efficiently used.
In the discharge area behind the corrugator the system exactly defines how and in which order and sequence the corrugated cardboard stacks reach the intermediate storage and the converting machines with an optimal utilization of the transport capacity.
These calculations are effected in real time and are the condition for continuous new evaluations of the prioritites of the individual operations.
The converting machines are supplied in time with goods for conversion according to the definitions of the ERP systems. After the conversion, the corrugated cardboard stacks are discharged from the machines and fed to the pallet protection. (picture 2) Here the correct pallet type is automatically prepared and the data for the strapping are available. The secured goods reach the finished goods storage and are ready for despatch.
The system flexibly reacts to inputs by the operators. During the entire production process the products can always be identified.
A dynamic visualization of the processes provides the customer an overview of the complete production flow.
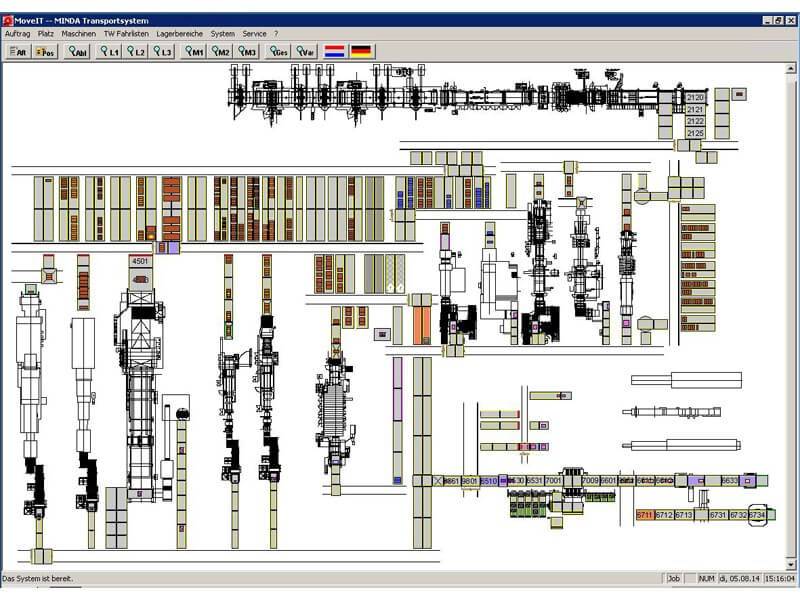