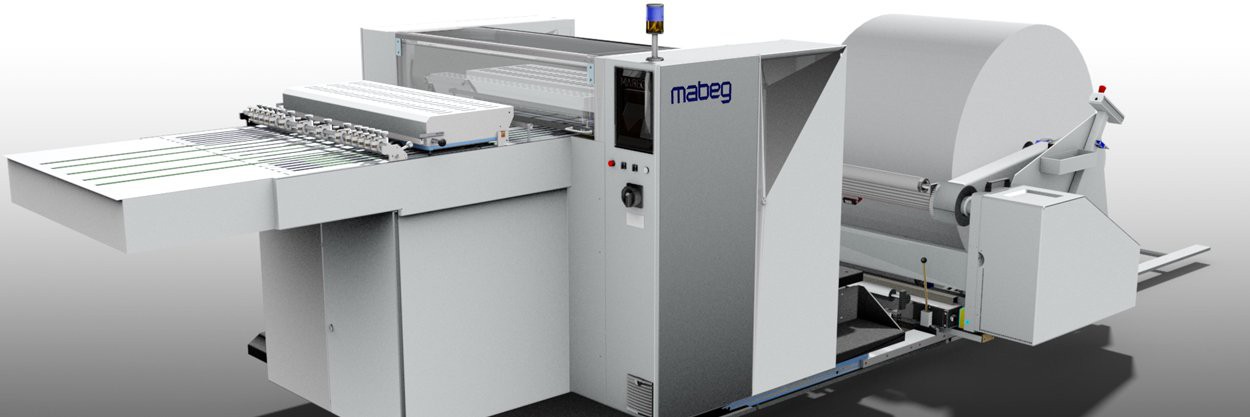
MABEG RS reel sheeter
Built to save you time and money
The MABEG RS reel sheeter (cross cutter) enables the use of sheet-fed printing presses for the processing of paper web, which is often far less expensive and easier to process than sheets. The web is cut into pieces of exactly the right length, thus preventing waste and in turn saving both resources and money. In addition to the financial benefit of using cost-efficient web, it is now unimaginable to do without reel sheeters when processing plastic film or lightweight paper.
More than 350 MABEG reel sheeters are in use around the world. They have been fitted to printing presses from all manufacturers, and have proven their reliability day in, day out in harsh industrial environments. The RS reel sheeter family now includes in-line reel sheeters designed for direct connection to sheet-fed offset presses for print formats 3B, 6 and 8.
Customers looking for a stand-alone reel sheeter with integrated sheet stacker need look no further than the MABEG RS 106X–TT–1S. It can be fitted with a camera-based register cutter, making it ideal for paper mills required to cut banknote paper relative to a watermark or cut mark, for example.
Click on one of the links to access more detailed information about the solutions we offer:
Four key customer benefits, four opportunities for savings
1. Processing of cost-efficient paper web on sheet-fed printing presses
- Reduced paper costs thanks to the use of less expensive paper web on sheet-fed printing presses
- Cutting of sheets straight off the reel in a single process step – the “money maker” for any face and reverse printing machine
- Processing of materials only available on reels
- Use of leftover reels from rotation presses
2. Reduction in paper consumption when processing special formats
•Sheets cut exactly to required length: sheet length adjustable in 0.1-mm steps using the touch screen
•No paper waste when processing print jobs involving special formats
•No need to order non-standard sheet sizes – all lengths are available on-demand
•The omission of a second gripper margin in Superperfektor printing presses can be translated directly into a reduction in paper consumption
3. Improved process reliability and enhanced performance due to the omission of sheet separation when printing lightweight paper
Potential applications include: medicine package inserts of up to 35 g/m².
The suction head is not used during web-fed operation. The sheet separation stage, which is often problematic when working with very thin material, is therefore rendered superfluous and the number of sheet stops and misaligned sheets in turn reduced.
During web-fed operation, each sheet is cut in-line and transported directly to the sheet feeder of the sheet-fed printing press. This helps ensure trouble-free, uninterrupted printing and higher process speeds.
Paper reels of low or medium paper weight contain many more sheets than sheet stacks do. The amount of stops and operator intervention required is therefore far lower.
What is more, the amount of set-up work required when changing the material is drastically reduced. To give an example, the MABEG RS makes it possible to switch from 35 g/m² to 180 g/m² paper with a minimum of adjustments and almost no run-up optimisation.
4. Improved process reliability and enhanced performance due to the omission of sheet separation when printing packaging
Thin films and aluminium-coated papers are becoming increasingly popular in the field of packaging printing. The majority of applications involve in-mould labels and other labels.
Electrostatic charging causes sheets of this type to adhere closely to one another. This makes sheet separation extremely difficult – if not impossible – and results in inadequate process reliability and speed.
MABEG reel sheeters are now able to achieve throughput rates in excess of 12,000 sheets per hour depending on the substrate involved. To give an example, this enables substrates with a thickness of as little as 50 µm to be processed on sheet-fed printing presses at very high levels of productivity. Our customers therefore benefit from a combination of the flexibility of sheet-fed printing presses and the cost advantages of web-fed printing.
In-line reel sheeters also allow substrates that are only available on rolls to be fed to sheet-fed printing presses. The optional Corona post-treatment system serves to ensure optimal ink receptivity in the printing press.